1.主要技术改造内容
1.1烟气净化除尘系统
转炉烟气净化除尘系统最初的工艺流程如图1所示:
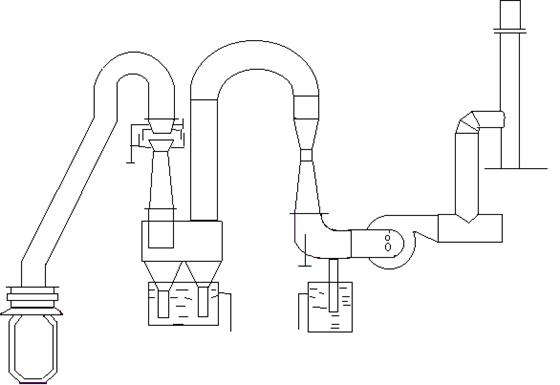
投产后,突出存在以下几个问题:
——除尘水质差:水温高、PH值>11,管道结垢严重,烟气量大,设备负担重。
——矩形可调喉口文氏管机构积灰严重。
——弯管脱水器因体积小、内部结构复杂,烟气冲刷处磨损严重且清灰难度大。
——烟气带水量大,脱水器能力小不能满足要求。
——随着冶炼强度增加,D700风机能力小抽气量不足,操作环境恶劣,且风机转子磨损严重,检修频繁。
——余热锅炉蒸汽回收系统回收量小,大部分蒸汽长期对空放散,形成能源浪费和噪声污染。
为实现安全、高效回收高质量转炉煤气,必须对转炉烟气净化除尘工艺进行适应性改造,以达到回收煤气的要求。
针对以上问题,从99年起相继对相关设备进行了改造。
为减少90°弯管脱水器堵塞,便于清灰操作,将二文前置于一文脱水器出口;二文R-D翻板可调结构改为重砣环缝式;将重砣由通常的顺装改为倒装,下置一个碗型喷嘴以代替原来的多喷嘴,解决了喷嘴堵塞带来的布水不均和多喷嘴检修困难等问题。
考虑到煤气回收后除尘水带煤气量较大,为安全起见,将原一文脱水器改为背包重力脱水器,使除尘水中的煤气有充分时间溢出,避免了水带煤气现象;二文脱水器为便于工人进行清灰操作,利用现场空间较大的条件,改型为下旋式旋流板脱水器;为加大脱水力度,在二文脱水器后增设复档旋风脱水器。
原一次除尘风机型号为D700,因长期不能满足炉前除尘要求,必须全部更换。通过建一拆一的方式,于2001年6月将三台主风机全部更换为AII1000型离心鼓风机。(备用风机也于2003年改造为AII1000型)。
为提高除尘水质,我公司先后投入了聚铁、聚铝等凝聚剂,并于2000年增设粗颗粒分离装置,投入运行后,对改善水质,降低污水碱度和PH值,减轻水处理设备负担起到了明显作用。采用定期投药的方式对除尘循环水PH值进行调整,使我厂除尘水PH值基本稳定在9左右,并对冷却塔布水结构进行了重新调整,使水温在原有基础上降低了10℃以上。除尘管道结垢情况有了很大程度的改善。
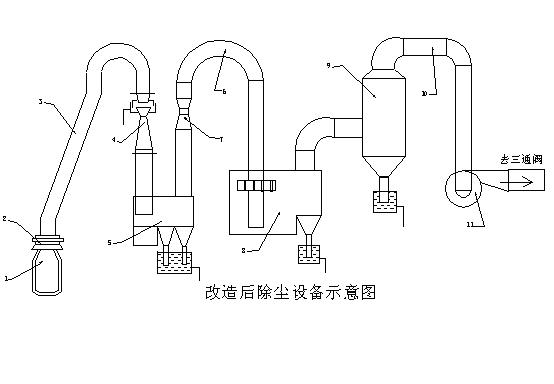
1.转炉炉口2.活动烟罩3.汽化冷却烟道4.一级溢流定径文氏管5.背包重力脱水器6.连接管道7.重砣环缝可调二级文氏管8.旋流板重力脱水器9.复档旋风脱水器10.负压管道11.AⅡ1000风机
1.2转炉煤气回收系统
由于炼钢厂设备在设计时预留了回收系统,因此设备衔接不存在问题。在不停产的情况下,在除尘风机后依次安装旁通阀、大管径三通切换阀、旋转水封阀、U型水封并在百米以外新建三万立干式煤气贮柜及相关设备。
转炉煤气是易燃、易爆、高毒性的气体,因此,系统安全监控与自动控制程序的确定对回收工作的安全运行至关重要。通过充分的考察调研,听取相关厂家回收工作中的经验教训,最终对煤气成份自动分析监控系统及煤气回收计算机控制软件进行了优选定型。
1.3综合利用
1.3.1转炉煤气的利用
随着轧钢生产线、白灰窑等新增项目逐年增多,原有煤气资源已不能满足需要。因此将转炉煤气尽快投入使用便成了公司发展生产的关键因素。合金烘烤、钢坯自动切割等对煤气热值要求较高的,仍然沿用焦炉煤气;转炉煤气主要单独或与高炉煤气混合使用。
2001年初开始铺设煤气管路,新建了一座高炉-转炉煤气混合站,轧钢加热炉则引进了成套的蓄热式燃烧系统,整套应用系统于2001年6月全部完工。
2.3.2除尘泥的利用
对一次除尘污泥(含铁40%左右)经过适当调整成分、焙干加工成复合造渣剂,供转炉化渣使用。增加了金属铁的回收利用,降低了其它造渣剂的用量,简化了辅料结构,同时杜绝了碱性除尘污泥外排对环境的污染。
2.主要技术特征
公司在实施转炉烟气净化回收与综合利用技术的过程中,为突出体现工艺的安全性与易操作性,引进开发了大量先进技术,实现了全微机联锁、自动监控回收,具有很高的安全性与自动化水平。
2.1煤气回收自动控制系统
煤气回收系统的可靠性将直接影响转炉的正常生产和煤气柜的安全。在综合考虑部分单位的回收状况后,我公司与北京航星自动控制有限公司合作开发了一整套煤气回收控制系统,并在实际应用中不断进行自我完善。该系统具有如下特点:
——回收计算机系统由两套西门子S7—300PLC进行控制,为提高系统的可靠性减少事故停机,采用了双PLC冗余配置。中央机架与远程站接口模块均采用一主一备,从而保证整个系统的安全稳定运行及通讯网的畅通。在进行I/O模块配置时,一个I/O模块仅分配一座转炉的I/O量,使三座转炉运行互不影响。
——自动回收控制程序考虑了所有影响安全回收的因素,充分利用回收设备功能完善,安全监控手段严密的特点,将回收条件设定为10个,回收中断条件更有13个之多,使回收工作的安全性大大提高。
——在程序设计中,考虑到我公司转炉操作不稳定煤气成分上下波动的现状,在程序中加入了计时器控制,避开回收初期残余煤气的影响;根据煤气成分可自动进行多次回收,既保证了煤气质量,又最大限度的提高了回收量。
——将回收分为三个档位,开始回收的CO含量值分别为30%、35%、38%,可根据用户的不同需求,灵活选取不同档位回收,以最大程度回收高质量转炉煤气。
系统运行至今,安全可靠,未出现任何安全隐患。
2.2二级文氏管结构优化
二文前置于一文出口,采用倒装重砣环缝式结构,下置单个碗型喷嘴代替原多喷嘴结构,杜绝了因喷嘴堵塞造成的布水不均,改善了除尘效果,大大减轻了喉口结垢情况,便于维护检修。
2.3系统压差调整
重砣调整采用液压控制系统,液晶数字显示重砣行程,远程集中控制,操作工在转炉主控室可根据炉前除尘状况,在冶炼操作中对炉口压差进行及时调整,以最大程度满足转炉生产与煤气回收的双重要求。
2.4旋流板脱水器
与上海智源综合利用设计有限公司合作,开发了下旋式旋流板脱水器以代替二文后90°弯管脱水器,该设计充分利用了离心力原理,使管道中煤气进入后,水分在叶片上充分撞击凝聚,再经旋流板导出。该项设计强化了水气分离,杜绝了原弯管脱水器除尘水被脱除后又被部分带出的弊端,脱水效果良好,并且脱水器内部空间大大增加,便于工人进行清灰操作,工人劳动强度大幅度降低。
2.5汽包(余热锅炉)串接技术
由于炼钢蒸汽瞬时发生量大,现用汽包容量小,在输出量小于发生量时,剩余蒸汽仍有对空放散情况,鉴于现场空间小,通过开发软水强制循环及完善汽包自动上水工艺,在保证系统安全的前提下,将三座转炉汽包在并联的基础上进行串联,利用三座转炉间歇生产的特点,将一座转炉暂时不能输出的蒸汽存储于相邻汽包,降低汽包内蒸汽压力峰值,功效等同于增加了一座汽包,使放散量大为减少,蒸汽回收量达到90公斤/吨钢以上。
2.6转炉氧枪喷头改造
氧枪喷头为三孔拉瓦尔型,通过对喷头参数进行修改,将喉口直径由26.4mm扩大为27.2mm,在供氧压力不变的情况下,氧流量增加400m3/h。冶炼强度增加,炉内C-O反应集中,转炉煤气的质与量较改造前均有提高:一次性回收时间平均增加2.8分钟,煤气最高CO含量也由65%增长为75%左右。
2.7其它相关技术
2.7.1复档旋风脱水器
在二文脱水器后增设复档旋风脱水器,加大脱水效率,减轻风机运行负载。
2.7.2 AII1000离心鼓风机
该风机运行平稳,投产后大大提高了烟气捕集能力,使煤气回收量及炉前工作环境大为改善。
2.7.3煤气回收成套设备
——YJ-SF型气动三通切换阀
——YJ-SN型气动水封逆止阀
——PF10气动旁通阀
该系列设备具有运行平稳、转换时间短、可采用手动或自动控制及多项安全报警系统等特点,能实现远距离集中控制。
2.7.4煤气贮柜及加压机
鉴于转炉煤气瞬间发生量大,要求气柜活塞升降速度快的特点,采用了威金斯干式煤气柜,活塞升降速度可达4m/min。可满足三座转炉同时回收的要求。我公司采用四台AI230加压机对外输送煤气,保证了不同用户对煤气压力及煤气量的需求。
2.7.5 ZD-101转炉煤气自动分析系统
该设备主要部件均为德国西门子产品,仪表指示稳定、精度高,分析速度极快,为煤气回收的安全运行提供了可靠的保证。
2.7.6煤气燃烧系统
两个轧钢工段加热炉均采用了蓄热式烧嘴供热方式,该系统的石球式蓄热室可以将空气及低热值转炉煤气同时加热至~1000℃。
2.7.7汽化冷却自动化控制系统
为确保汽化上水及蒸汽回收工艺的安全性及质量,对原汽化操作系统进行了自动化改造,采用S7-400PLC进行控制,操作简单,基本实现了无人职守。
2.7.8转炉污泥成球作炼钢造渣剂技术
该技术以转炉除尘污泥为基体,掺加废石灰末等碱性物料,用少量能源制成球团,是一种良好的炼钢造渣材料。该技术工艺简单、效果显著,具有良好的环境和经济效益。
2.7.9转炉音平控渣系统
为提高降罩操作时转炉操作的稳定性,增强岗位工对炉内反应状况的掌握,配套使用了三套转炉音平控渣系统。该系统通过在炉口附近采集冶炼不同时期炉内传出的声音信号,再通过音平仪将音平信号转换为电信号,在显示器上以曲线的方式将炉内渣层厚度及泡沫化状况直观的反映出来。可帮助摇炉工对炉内反应进行预判,提前控制,以提高转炉化渣水平。
3.系统改造前后基本情况
技术应用前后主要工艺对比情况见表-1
表-1 技术应用前后工艺对比
序号
|
项目
|
技术应用前
|
技术应用后
|
1
|
文氏管
|
一级溢流可调文氏管(矩形喉口),R-D米粒翻板可调二级文氏管
|
一文为定径(φ600mm)文氏管,二文前置并改为倒装重砣环缝式单喷嘴结构
|
2
|
脱水器
|
90°弯头脱水器
|
一文后改为背包重力脱水器,二文后旋流板重力脱水器加复档旋风脱水器
|
3
|
一次除尘风机
|
D700离心鼓风机
|
AII1000离心鼓风机
|
4
|
蒸汽回收
|
汽包并联回收
|
汽包在并联基础上串联回收
|
5
|
转炉煤气回收
|
全部对空放散
|
绝大部分回收
|
6
|
除尘污泥
|
全部外排
|
加工后循环使用
|
7
|
汽化冷却系统
|
人工监控操作
|
全自动监控,无人职守
|
8
|
转炉煤气应用
|
无
|
应用于带钢及棒材加热炉
|
9
|
转炉氧枪喷头
|
喉口直径26.4mm
|
喉口直径27.2mm
|
4.应用效果
4.1净化除尘系统相关工艺参数见表-2
表-2 净化除尘系统相关工艺参数
项目
|
技术应用前
|
技术应用后
|
风机运行情况
|
作业率96~97%,风机转子使用周期一个月
|
作业率99.2%,风机转子使用周期三个月
|
系统结垢情况
|
0.5mm/炉左右
|
<0.1mm/炉
|
除尘水PH值
|
>11
|
<9
|
烟气含尘量
|
>300mg/Nm3
|
<120mg/Nm3
|
炉前除尘情况
|
差
|
良好
|
4.2煤气回收
煤气回收系统于2001年4月投入运行后,回收量增长迅速,目前每炉平均回收时间在6′20″以上,最高回收时间大于9分钟,已具备单炉100m3/t钢的回收水平。由于煤气用户还在进一步开发中,目前煤气回收率保持在80%以上,整体回收能力在75m3/t钢以上。
4.3综合利用
回收的转炉煤气经加压站加压,一部分直接供棒材加热炉,另一部分与高炉煤气混合,送活性白灰窑与带钢加热炉。目前,使用效果良好均能达到相关工艺要求。化渣球经试用,完全满足炼钢操作的需要,年用量可达3.15万吨,回收金属铁1.27万吨。
5.对社会经济发展和科技进步的意义
5.1通过对再生能源(转炉煤气、蒸汽、除尘泥)回收利用,年创经济效益两千余万元。
5.2扩大了能源供应,满足了新建工程对煤气能源的需求。
5.3通过完善湿法净化除尘系统设备,使烟气含尘量减少到120mg/m3以下,蒸汽放散噪音大大降低,系统结垢情况明显减少,自动化监控系统运行安全可靠,降低了工人劳动强度,改善了工作环境。
5.4减少烟气、除尘泥外排,保护了环境,为全面实现清洁生产打下了基础。
转炉烟气净化回收与综合利用技术的实现,促进企业设备管理及工艺管理水平的全面提高。通过对转炉再生能源的回收利用,一方面解决了冶金企业发展生产最重要的能源需求问题,另外,对炼钢厂节能与环保工作的进步起到了重大推动作用。
6.存在的问题
6.1进一步开发转炉煤气新用户,提高自动配比水平,确保煤气热值的稳定性,以便将转炉煤气推广到热力厂55t/h锅炉及白灰窑的使用上,将煤气回收率提高到95%以上。
6.2对现有复档旋风脱水器结构进行改造,以进一步提高煤气的清洁度。
6.3增加整套除尘系统的气密性,提高炉口压差控制水平,使转炉煤气平均CO含量提高至55%以上,最高含量达到85%以上。