2012年,世界经济持续处于缓慢恢复状态,各国企业经营困难增加,需求变化多样性。目前世界加工制造业正在逐步尝试由传统的大量生产、批量生产方式向多品种小批量生产方式转化,因此各制造企业纷纷把目光投向了更适用于小批量、多品种、低消耗的生产管理模式:精益生产。
明睿管理咨询基于精益生产的理论,拟对现场改善的方法进行研究,并得出一套现场改善的方法,最后对企业的生产现场及样板线的改善进行分析,验证所提出的现场改善应用方法的有效性和实用性。理论结合实践,不让精益生产之是企业的表面功夫。
一、理论结合实际,建立生产现场改善的方法体系
现场改善可以理解为现场管理优化,运用现场管理的手法对生产现场的人、机、料、法、环等各生产要素进行持续的改善。实行现场改善活动,可以保证产品质量;消除各个环节的浪费,降低成本;改善工作环境,提高工作效率。明睿管理咨询把管理的方法融人改善之中,结合工业工程理论及精益生产理论对方法研究、作业测定、生产线平衡、5S活动、定置管理、目视管理、班组管理等的归纳总结,构建了生产现场改善的方法体系图,如图1所示。
一、理论结合实际,建立生产现场改善的方法体系
现场改善可以理解为现场管理优化,运用现场管理的手法对生产现场的人、机、料、法、环等各生产要素进行持续的改善。实行现场改善活动,可以保证产品质量;消除各个环节的浪费,降低成本;改善工作环境,提高工作效率。明睿管理咨询把管理的方法融人改善之中,结合工业工程理论及精益生产理论对方法研究、作业测定、生产线平衡、5S活动、定置管理、目视管理、班组管理等的归纳总结,构建了生产现场改善的方法体系图,如图1所示。
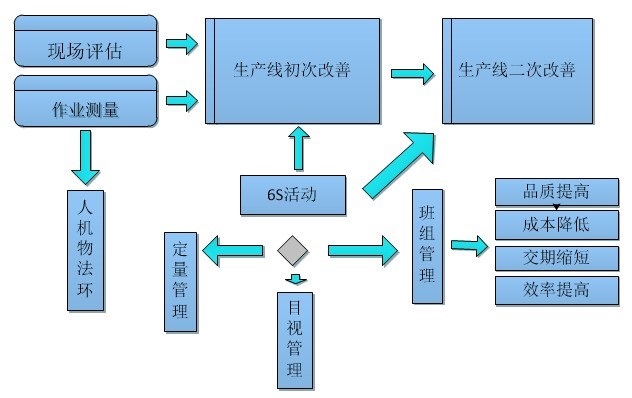
二、实践检验体系,生产现场改善方法体系的应用
现场是"企业为顾客设计、生产和销售产品或提供服务的场所"。在制造业,现场一般指生产部门的制造现场。现场改善就是"对生产现场进行综合治理,运用科学的管理思想、方法和手段,对生产现场的各种要素进行合理配置和优化组合的动态过程"。应用生产现场改善的方法体系,实行现场改善活动,可以保证产品质量;消除各个环节的浪费,降低成本;改善工作环境,提高工作效率;达到生产线平衡。
1、现场评估、作业测量
在生产现场改善前,应该对生产现场进行现场评估和作业测量,其中,包括后现场LAYOUT、人员配置与生产状况、工序能力调查、现状物与情报流等的人、机、物、法、环的评估。只有对生产现场进行实事求是的评估和测定,全面掌握和认识现况,才能对生产现场进行有目的、有方向的改进。
2、 6S活动的应用
实施"6s"现场管理,要不断进行整理、整顿、清扫、清洁、素养、安全,并逐步循环和提高。整理就是要妥善处理现场的停滞物品,分离废弃物和保留物;整顿是将整理后需要的物品定点摆放,把有用物归类,各就各位,以期达到合理布置、方便使用,且提高安全性、实现目标管理;清扫就是要求全体人员自己动手清扫,创造一个干净、明快舒适的工作环境;清洁是对整理、整顿、清扫这3项工作的保持和坚持;素养是规范人的行为,养成自觉执行制度和作业标准的良好习惯。
3、生产现场的改善
由图l可知,只有做好前期的作业测定、5s活动、定置管理、目视管理、班组管理等各环节的基础上,才能谈到真正意义上的生产现场的改善。因为只有真正把现场的实况完全掌握好,才能把现场的方方面面的问题的源头掌握住;只有把现场真正目视化了,问题才一目了然地呈现出来。当然,某些难以用肉眼、用感觉或凭经验就解决的问题,就需要借助于一些数学统计分析技术、工业工程技术等等,如X-R图、时间观察表、工程山积表、CT/TT分析等。
① 改善方案的确定
根据对生产线现场的现场评估和作业测定确定其改善方案,如表1所示。
改善方案
|
||
类别
|
问题
|
实行方案
|
品质提升
|
1.制程报废0.5%(主要是人员操作不良)
|
对产线人员进行培训,提高操作熟练度
|
2.专机不良率高(人员未及时换刀)
|
修订换刀频率
|
|
库存降低
|
3.毛胚送货批量较高
|
寻找适合毛胚供应商
|
生产性
|
4.粗车一(35秒/件)人员利用率低
|
合并为一人作业
|
5.粗车二(180秒/件)人员利用率低
|
||
6.精车一(40秒/件)人员利用率低
|
||
7.精车二(100秒/件)人员利用率低
|
||
8.钻孔(60秒/件)人员利用率低
|
合并为一人作业
|
|
9.专机(135秒/件)人员利用率低
|
||
10.打字(20秒/件)人员利用率低
|
||
11.瓶颈工序-专机工序故障率较高
|
作为关键设备管理,建立异常登记表
|
|
12.人员操作能力单一
|
训练多能
|
②实施改善方案的效果
LAYOUT改善对比如图4所示。其整体效果如表2所示。
整体效果对照表 |
||||
项次
|
改善前
|
改善后
|
效果
|
实施
|
人员
|
4人
|
2人
|
节省2人
|
完成
|
材料
|
无固定数量
|
定位放置、流程架实用
|
作业方便、效率提升
|
完成
|
设备
|
未使用流程架
|
使用流程架
|
省力化
|
完成
|
作业方法
|
没有标准作业
|
建立标准作业2个
|
产线有标准作业
|
完成
|
在制品库存
|
数量无规划,任意放置
|
标准持量:2件
|
库存量最低标准:2件
|
完成
|
③残留问题点及后续改善方向
通过前期的改善,无论品质、生产效率、还是在制品库存,各方面都有了很大的改善效果;但同时也找到了不足之处和残留问题点,这也为后续改善提供了方向。进一步改善的残留问题点如表3所示。
残留问题
|
||
类别
|
存在问题
|
实行方案
|
品质提升
|
1.换刀频率不合理
|
观察换刀情况,统计换刀数据,以品质最大化和成本最小化简历换刀周期的数学模型。设定产品的换刀周期
|
人员
|
2.虽然精简2人,但操作者技能还没跟得上工艺要求
|
继续定期对产线人员进行培训,提高操作熟练度
|
三、总结
基于精益生产方式的现场管理,通过作业测定、生产线平衡、5s活动、定置管理、目视管理、班组管理等各环节,使其精益、高效的理念得到全方位的体现,从而使生产现场的持续改善成为确保提升企业竞争力的一种关键要素。
明睿管理咨询提出这一模式的目的在于为制造业(特别是汽车制造业)提供一种区别于模仿国外汽车企业的精益生产模式的发展思路,建立符合其自身循序渐进发展规律的、精益的生产现场改善理念和发展规划。